How to determine an accurate endpoint of high-shear mixer granulation
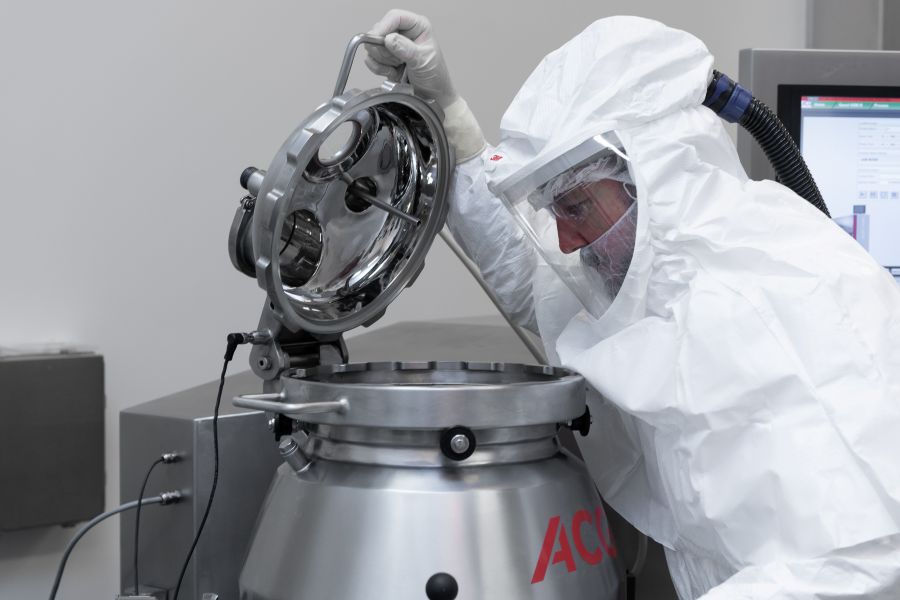
The challenges of endpoint determination in HSM granulation
Wet granulation accounts for over 70% of the world's granulation processes, with the high-shear mixer as the preferred approach. However, formulation scientists continue to seek more reliable methods to determine the exact endpoint of HSM granulation. Knowing when ideal granules have formed is crucial for ensuring seamless tablet compression and achieving the desired tablet properties. Key pre-compression qualities impacted at this stage include granule strength, bulk density, particle size distribution, and flowability.
Although researchers have developed various predictive techniques and equipment manufacturers have introduced upgrades, HSM granulation still relies heavily on empirical methods for endpoint determination. This often results in inconsistencies, such as under- or over-granulated material, which can cause problems in later manufacturing stages. Many operators still continue to use traditional manual testing to evaluate the granules, but this subjective approach frequently leads to inaccuracies.
Achieving consistent endpoints is essential, requiring precise control over process variables. For any given set of parameters, the endpoint is typically assessed by measuring properties such as granule strength, density, and mean particle size distribution. However, for optimal results, an ideal endpoint determination technique should offer accuracy and reproducibility while accounting for changes in process variables, including mixer geometry, blade speed, batch size, and binder addition methods.
The key phases of HSM granulation include dry mixing, binder addition or spraying, and wet mixing. While the wet mixing phase plays the most significant role in defining the endpoint, binder addition also substantially influences granule formation through nucleation, densification, and growth. To precisely determine when the endpoint is reached, both phases must be considered.
A common method involves monitoring the resistance experienced by the impeller (reflected in the current drawn by the motor). Results are typically recorded within a set range to achieve the desired granule quality. Given that HSM offers a broad particle size distribution, precise endpoint determination is vital for consistency.
Current methods for determining the endpoint in HSM granulation
Wet mixing duration
As one of the oldest techniques for determining the granulation endpoint, this method depends on the duration of wet mixing step after adding the binder. However, it can lead to unreliable results if there are variations in the properties of the starting materials, especially when changing suppliers. Manual binder addition also introduces potential errors in timing and quantity, affecting batch-to-batch consistency.
Power consumption monitoring
This cost-effective method measures the power drawn by the mixer’s motor (in amperes). The results obtained can be correlated to granule growth. An increase in powder mixture consistency generates greater resistance on the granulator blades, which affects power usage. However, the readings are influenced by many factors, including raw material properties, equipment type, process variables, and mechanical wear. Critically, this method measures the load on the motor, not the impeller itself, and readings can fluctuate regardless of the actual process.
Calculated torque
Calculated torque offers another means of monitoring the endpoint, derived from the motor’s current. Since HSMs use alternating current induction motors, measurements often fluctuate, limiting accuracy. Any inaccuracies in current readings directly affect torque calculations.
Reaction torque measurement
When the impeller shaft rotates, the motor tries to move in the opposite direction but is unable to because it is securely bolted in place. The tension in the stationary motor base can be measured using a reaction torque transducer. However, the fluctuations that occur during the wet mixing phase make it challenging to obtain accurate readings, which can compromise reliability.
Torque rheometer
A torque rheometer offers an offline assessment of the torque needed to rotate device blades and gauge the rheological properties of wet granules. However, as an offline method, it cannot provide real-time or in-process endpoint analysis.
Acoustic emission
This approach uses piezo-electric acoustic emission sensors to detect the endpoint of the granulation process. The indicators provided by the acoustic transducer help monitor changes in particle size, flowability, and compression properties. While non-invasive and sensitive, this technique can be quite expensive.
Near-infrared spectroscopy
NIR sensors measure moisture content during granulation but are not always precise for determining the exact endpoint.
Focused beam reflectance measurement
This technique determines particle size using a laser beam focused near a sapphire window on a probe. The chord length distribution (CLD) can be converted to represent either the number-based or volume-weighted particle size distribution. In many cases, CLD measurements are sufficient for tracking dynamic changes in particle size, shape, concentration, and rheology during a process. While this method is effective, it is also expensive. However, it remains a valuable tool for real-time monitoring of particle characteristics in various applications.
Direct torque measurement
Direct torque measurement enables real-time tracking of the impeller’s torque in Newton metres (Nm) via a sensor mounted directly on the impeller drive shaft. Unlike traditional torque calculations based on current consumption, this technique eliminates error sources such as bearing wear, gear degradation, oil viscosity, and temperature fluctuations. It thus provides superior accuracy and process control.
Torque sensors employ strain gauges fitted to rotating parts, utilizing rings, wireless telemetry, or rotary transformers. The technique is based on measuring how much force is needed to turn the impeller shaft. When torque is applied, the shaft twists slightly, causing a stretch at a 45° angle to its axis. Torque transducers detect and measure these changes using bonded strain gauges, providing an accurate reading of the applied torque.
Essential tools for direct torque measurement
To ensure accurate and efficient direct torque measurement, the following tools are essential
- A direct torque measuring device, with a contactless sender and receiver integrated into the impeller shaft
- A pre-calibrated instrument
- An HMI (Human-Machine Interface) display for real-time values
- Granulation endpoint determination functionality
- Pre-set points for endpoint detection programmed on the HMI
Final thoughts
While rapid advances in technology have transformed many industries, pharmaceutical operations often retain conventional practices, especially in processes as critical as granulation. Determining the endpoint with accuracy is essential for effective tablet compression and final product quality. Though various traditional approaches still see widespread use, many lack the precision required for optimum results.
Direct torque measurement stands out as a reliable, accurate alternative for granulation endpoint determination, offering real-time process insight to help manufacturers not only achieve consistency but also address regulatory expectations. By integrating this technique, the industry can move towards greater excellence, ensuring each batch meets the highest quality standards.